AlTiN coating & TiAlN coating
For maximum tool life and thermal loads
AlTiN coatings, also known as altin coatings, increase the service life and durability of tools through high hardness and temperature resistance. These coatings made of aluminum, titanium and nitrogen are indispensable for demanding industrial applications. In the article you can read about their advantages, applications and differences to TiAlN coatings.
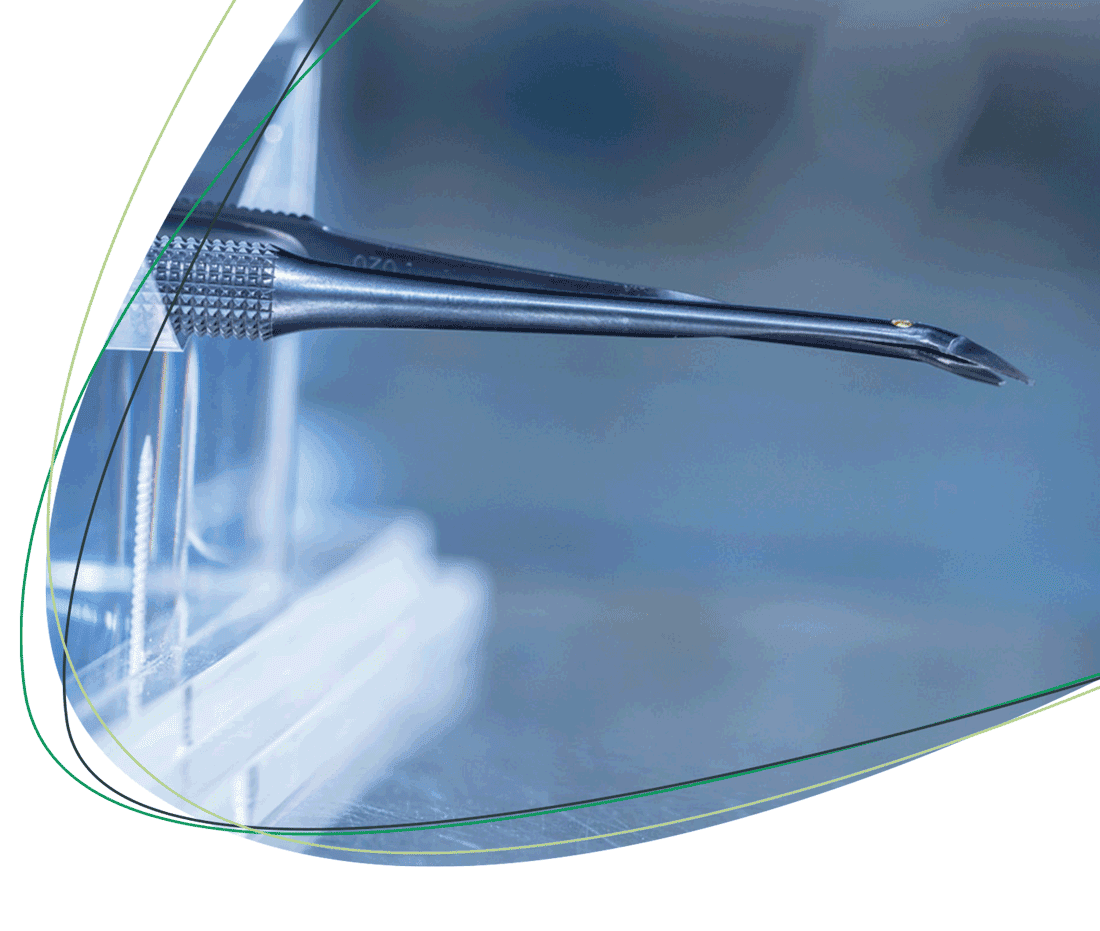
What are AlTiN and TiAlN coatings?
AlTiN and TiAlN coatings are advanced technologies developed for high performance industrial applications. Both coatings consist mainly of aluminum, titanium and nitrogen, with the ratio of aluminum to titanium varying. This chemical composition gives the coatings their outstanding properties. The basic elements of these coatings are aluminum, titanium and nitrogen, which are present in a special chemical compound.
The AlTiN coating, a combination of aluminium, titanium and nitrogen, is characterized by its high hardness and temperature resistance. A remarkable property of this coating is its ability to retain its hardness even at high temperatures. This makes it ideal for applications that are subject to high thermal loads.
On the other hand, the TiAlN coating has a higher titanium-to-aluminum ratio, which also gives it excellent properties in terms of hardness and thermal stability. Both coatings offer high resistance to oxidation, which makes them suitable for various industrial applications.
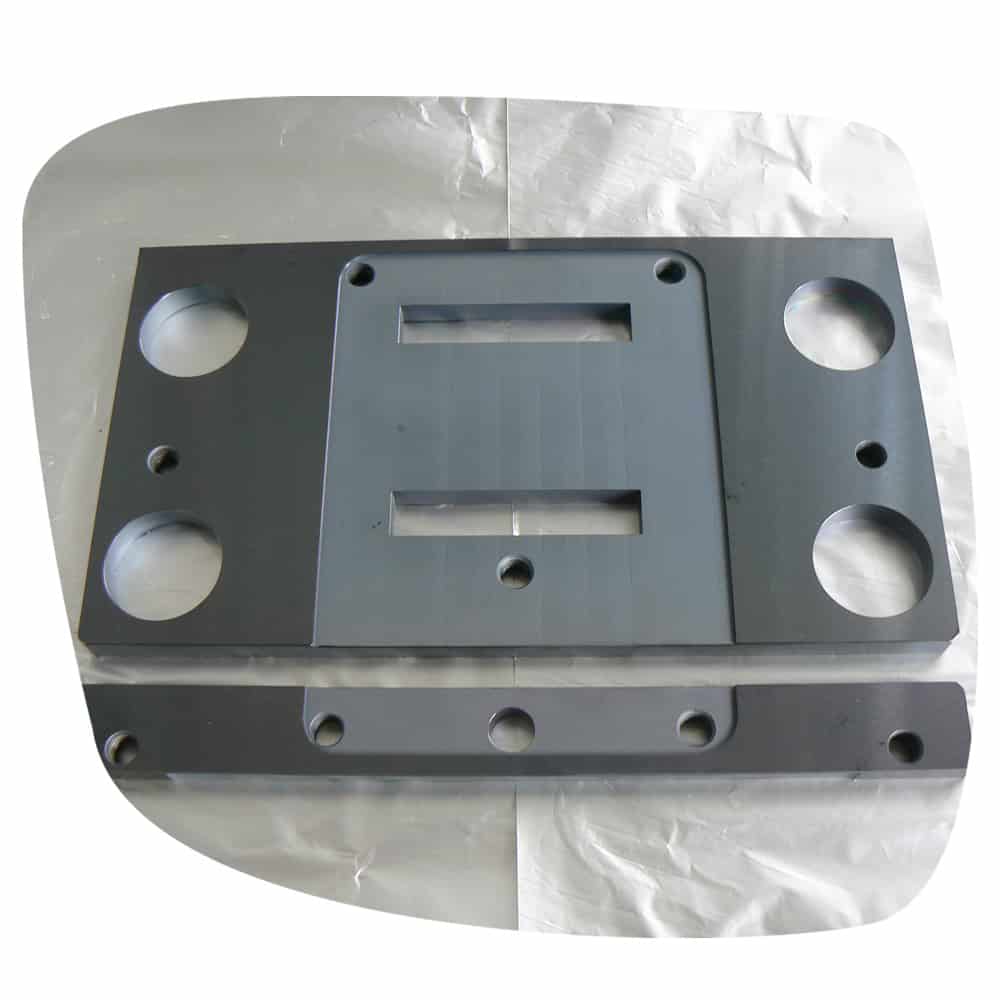
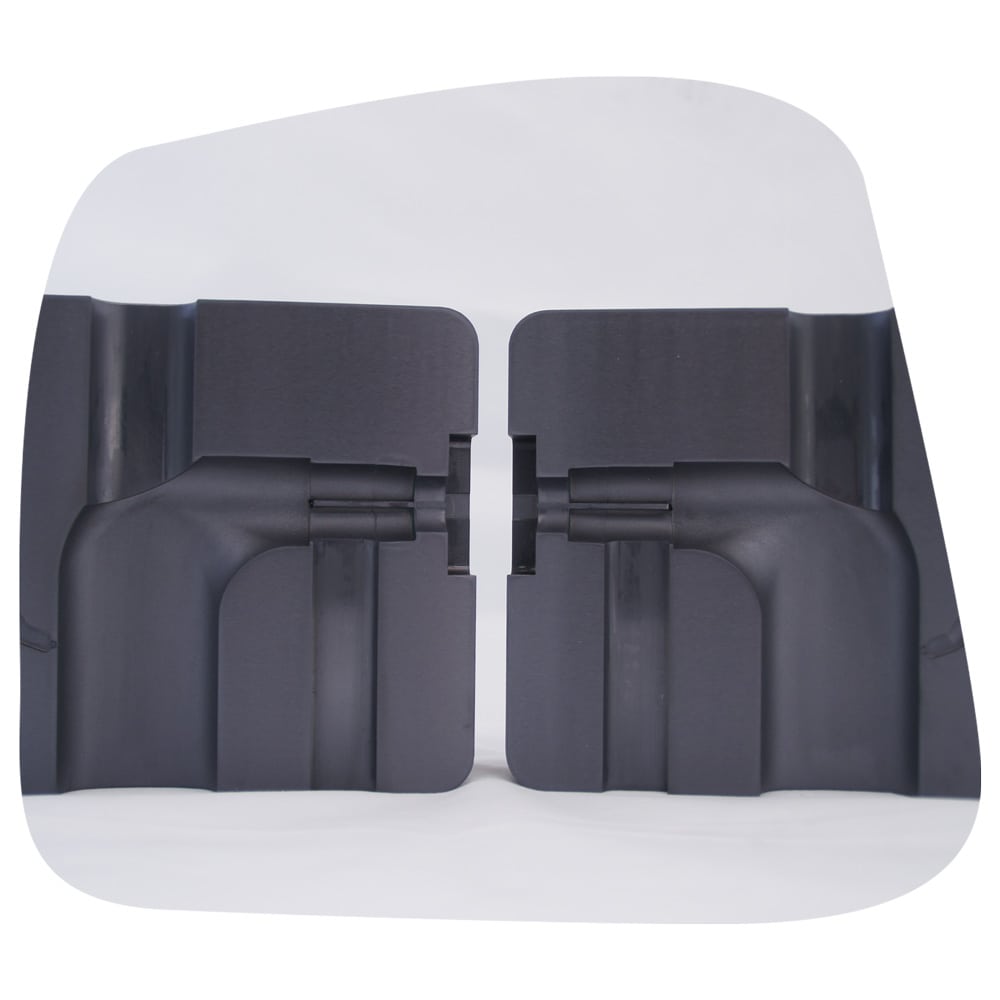
Advantages of AlTiN and TiAlN coatings
The use of AlTiN and TiAlN coatings has numerous advantages. One of the biggest advantages of the AlTiN coating is the significant increase in tool life. These coatings consist of several thin layers that together form a robust coating system. This is achieved by reducing friction during operation, which significantly increases the efficiency of the tools.
Another key advantage of the AlTiN coating is the ability to achieve higher cutting speeds. This not only improves machining efficiency, but also overall productivity. In addition, the AlTiN coating offers a higher nano-hardness, making it particularly suitable for milling very hard materials.
In addition to these general benefits, AlTiN and TiAlN coatings also offer specific advantages such as oxidation resistance and corrosion protection. These properties help tools stay sharp for longer and are less susceptible to wear, resulting in extended tool life of up to 14 times that of uncoated tools.
Areas of application for AlTiN and TiAlN coatings
AlTiN and TiAlN coatings are suitable for a wide range of applications, especially for machining hard materials. These coatings are ideal for high-alloy steels and titanium alloys machined in the aerospace industry. The improved wear resistance ensures that the tools remain sharp for longer and work efficiently.
These coatings are also widely used in the automotive industry and in injection molding. They provide the necessary heat dissipation and hardness to enable high cutting speeds, which is crucial in these industries. The ideal suitability for HSC (High-Speed Cutting) and HPC (High-Performance Cutting) machining as well as hss machining makes them indispensable for precise and fast machining processes.
In addition, AlTiN and TiAlN coatings are suitable for various machining processes such as milling, drilling, reaming and forming tools. For drilling and threading in particular, these coatings offer significant advantages in terms of tool life and efficiency. This versatility makes them a preferred choice for many industries that rely on tool efficiency and durability.
Technical comparison: AlTiN vs. TiAlN
To better understand the differences between AlTiN and TiAlN coatings, a direct technical comparison is helpful. The nano-hardness of AlTiN is around 38 GPa, while TiAlN has a nano-hardness of around 35 GPa. This difference makes AlTiN particularly suitable for applications that require a higher hardness.
In terms of the coefficient of friction, both are roughly the same at 0.35-0.37. The temperature resistance of AlTiN is up to 900 °C, while TiAlN has a temperature resistance of around 850 °C. At temperatures above 800 °C, the first signs of oxidation can occur. The first signs of oxidation can occur at temperatures above 800 °C.
Another important aspect is the behavior under dry machining and impact load. While both coatings are designed for high cutting speeds and thermal stability, AlTiN performs better at extreme temperatures on the surface. The AlTiN coating is particularly suitable for machining hard materials such as steel and stainless steel, making it ideal for dry machining applications.
Layer thickness and its significance
The coating thickness is a decisive factor for the performance of AlTiN and TiAlN coatings. An optimum coating thickness is in the range of 2 to 3 μm. This thickness offers a perfect balance between wear resistance and stress behavior.
A coating that is too thin can have a negative impact on wear resistance and tool life, while a coating that is too thick can impair stress behavior and heat dissipation. It is therefore important to choose the right coating thickness for the respective application in order to achieve the best possible performance.
The hardness-toughness balance is also a critical factor that is influenced by coating thickness. A well-balanced coating thickness can help tools remain both hard and tough, significantly improving their overall performance and service life.
Role of cooling in AlTiN and TiAlN tools
Cooling plays a key role in the use of AlTiN and TiAlN coatings. The use of coolant can significantly extend the service life of tools and improve machining performance. There are differences in the thermal behavior of the two coatings.
While AlTiN coatings are ideal for dry machining applications, TiAlN coatings can benefit from the use of coolants. The effects on tool life and machining performance are significant, as cooling helps to control temperatures and thus minimize wear.
Minimum quantity lubrication (MQL) is another method that can be used with both coatings to increase efficiency and extend tool life. This technique reduces the amount of lubricant required, which offers both economic and environmental benefits.
Practical examples: Coatings in use
The advantages of AlTiN and TiAlN coatings are best illustrated by specific practical examples. In the aerospace industry, these coatings significantly extend tool life and improve precision in series production. When machining steel in particular, these coatings significantly extend tool life. This leads to greater efficiency and lower costs.
In the automotive industry, these coatings help to improve machining processes by extending the service life of tools and increasing productivity. AlTiN and TiAlN coatings also ensure more precise and durable tools in medical technology, which increases the quality of the manufactured products.
These practical examples clearly show how versatile and effective AlTiN and TiAlN coatings can be used in various industries. They not only offer considerable added value, but also contribute to improving the entire production process.
B-Protect® (AlTiN) high-performance coatings
The world of coatings for tools is complex, but the benefits of AlTiN and TiAlN coatings are clear and compelling. These advanced coatings offer a combination of hardness, temperature resistance and wear resistance that make them indispensable for a wide range of industrial applications. From machining high-alloy steels in the aerospace industry to improving efficiency in the automotive industry, the applications are diverse and impressive.
Through the technical comparison, we were able to highlight the differences between AlTiN and TiAlN and show which coating is best suited for which application. We also highlighted the importance of coating thickness and cooling to ensure optimum tool performance. Practical examples from different industries have turned the theoretical advantages into tangible results, showing how crucial these coatings are for industrial production.
Our premium solution B-Protect® combines the best properties of AlTiN and TiAlN and offers customized solutions for specific requirements. With the advice of our experts, you can ensure that your tools are optimally protected and efficient. Do not hesitate to contact us and discover the benefits of B-Protect® for your applications.
B-Protect®: Our premium solution with AlTiN characteristics
Our premium solution B-Protect® combines the best properties of AlTiN and TiAlN coatings. This PVD coating consists of a combination of aluminum and titanium nitride and offers a hardness of up to 3,300 HV. The temperature resistance extends up to 900 °C, making it ideal for high-temperature applications.
The color characteristics of B-Protect® range from violet to black, which also visually indicates a high-quality color. This coating is particularly suitable for dry machining and minimum quantity lubrication (MQL), which means it can be used in many industrial processes.
B-Protect® is used in machining, injection molding and forming processes. This versatile coating solution offers excellent wear resistance and significantly extends the service life of tools. Art.
The most important facts at a glance
AlTiN and TiAlN coatings are advanced technologies that combine aluminum, titanium and nitrogen to provide excellent hardness and thermal stability. These coatings are suitable for high operating temperatures and various materials.
The use of these coatings significantly extends tool life, improves machining efficiency and reduces wear, resulting in significant benefits for industries such as aerospace and automotive.
The choice between AlTiN and TiAlN depends on specific applications, with AlTiN being suitable for high temperatures and TiAlN for low friction properties.